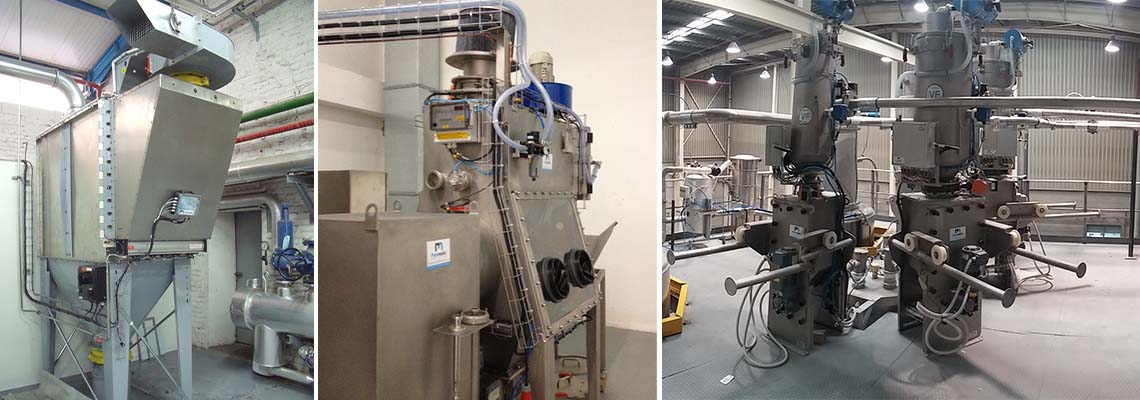
En cualquier instalación de producción, el control y la captación de polvo son factores clave para garantizar un lugar de trabajo seguro y saludable para los operarios. Hay una serie de dispositivos y tipos de equipos que pueden conseguirlo, que se detallan a continuación.
1. Anillos Pouyès / anillos de captación de polvo
Los anillos de colección de polvo, también conocidos como anillos Pouyès, se utilizan en los puntos de carga de material que requieren una operación manual. Los operarios pueden tener que cargar los materiales directamente en una tolva de almacenamiento o en un tanque de mezcla. Los anillos de Pouyès son colectores de polvo para tanques de carga, reactores o contenedores cilíndricos.
Los anillos de recogida de polvo protegen el entorno de trabajo del operario capturando las partículas directamente en la fuente de emisión. Su sencillo diseño consiste en una entrada abierta con una brida de conexión inferior y una espiga para conectar una manguera a un sistema central de recogida de polvo. Al crear un vacío en la atmósfera circundante, el polvo se captura cuando el material pasa por la entrada.
Se utilizan habitualmente en los siguientes tipos de operaciones:
- Llenado de tolvas con pequeñas bolsas de polvo.
- Reactores de carga
- Llenado de tambores
- Alrededor de la entrada de una mezcladora
- Limpieza del polvo de los puestos de trabajo
2. Confinamiento físico
Una forma de evitar que las partículas finas floten libremente por su planta de producción es diseñar equipos estancos al polvo. Uno de los mejores ejemplos son las estaciones de vertido de sacos y big bags. Normalmente, estas unidades están diseñadas para que el operario pueda abrir una puerta de acceso para separar la boca de descarga de un big bag o, en el caso de las bandejas de sacos, para cargar el saco directamente en la bandeja en la estación de descarga. A continuación, el operador debe abrir manualmente el contenedor para liberar el material.
Las cajas de guantes pueden utilizarse para proporcionar una barrera física entre el operador y el contenedor. Al disponer de una ventana de cristal con accesorios para los guantes, el operario puede cortar o separar el saco y evitar la exposición o el contacto directo con el material del interior. Del mismo modo, rodear el equipo de producción con un campo de contención de poliglás puede aislar aún más la zona circundante de la exposición a partículas tóxicas.
3. Transferencia de vacío
Hay varias formas de transferir los polvos desde el punto de carga en su planta hasta su destino final de envasado. El transporte mecánico, el transporte neumático, los transportadores de tornillo, etc., se utilizan de alguna manera entre los equipos de producción y algunos tienden a producir más polvo que otros.
Sin embargo, el transporte por vacío es uno de los métodos más limpios para transportar materiales secos. Incluso si tiene un sistema de tuberías con fugas, la fuga será de fuera hacia dentro. Con los sistemas de transporte a presión, la fuga se produciría desde el interior hacia el exterior, lo que provocaría derrames de material y polvo a la atmósfera. La razón es sencilla: al hacer el vacío desde la fuente de suministro hasta el punto de entrega, prácticamente no hay posibilidad de que el material se escape de las tuberías. Además, al utilizar un ciclón al final del sistema de transporte de material, se puede incorporar un filtro de polvo directamente en la parte superior de la tolva de recogida. Las partículas pesadas giran alrededor del ciclón y se depositan en el fondo, mientras que el aire sucio es separado y limpiado por el filtro de la parte superior. De este modo, el aire limpio llega a la bomba de vacío, manteniendo la zona limpia y la bomba en excelente estado de funcionamiento.
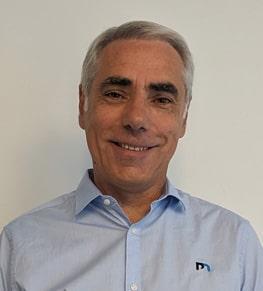
¿Necesita asesoramiento sobre el espolvoreo o
la dosificación? Estoy disponible para discutir el tema.
Orlando, experto en polvos
4. Colector central de polvo
En un colector de polvo central, el polvo se separa de la corriente de aire mediante elementos filtrantes planos y plegados. Un proveedor de equipos de filtración de polvo debe calcular todos los puntos de recogida necesarios y el flujo de aire en pies cúbicos por minuto (CFM) requerido para extraer la cantidad de aire necesaria en una unidad central.
El corazón del sistema es el filtro de mangas central, que consta de una carcasa de acero, elementos filtrantes insertados horizontal o verticalmente, una tolva de recogida para la eliminación del polvo y un sistema neumático de limpieza por chorro de aire inverso integrado en la puerta de acceso al filtro. Todos los componentes, incluidos el tamaño y la capacidad del ventilador del colector central de polvo, se diseñan en función de las necesidades de la instalación de producción. En general, está sobredimensionado para permitir futuras ampliaciones del proceso y conexiones del sistema.
5. Línea de proceso DosingMatic
Palamatic Process ha diseñado un sistema automatizado de dosificación de ingredientes llave en mano: DosingMatic®. Este sistema está diseñado para preparar y equilibrar todos los ingredientes secos en lotes pesados. La cabina de dosificación se desplaza automáticamente bajo las tolvas de dosificación por pérdida de peso y se llena con dosificadores de tornillo. Así, los ingredientes se preparan en una tolva de pesaje móvil y se trasladan a un punto de conexión posterior (sistema de transporte neumático, transportador de tornillo, mezclador, etc.). Las células de pesaje incorporan un volumen de almacenamiento intermedio que oscila entre 50 y 300 litros, en función de las necesidades de cada receta. El sistema puede diseñarse para incorporar de 10 a 40 tolvas de carga.
Al automatizar la dosificación de ingredientes secos de forma contenida, se reduce en gran medida la exposición al polvo.