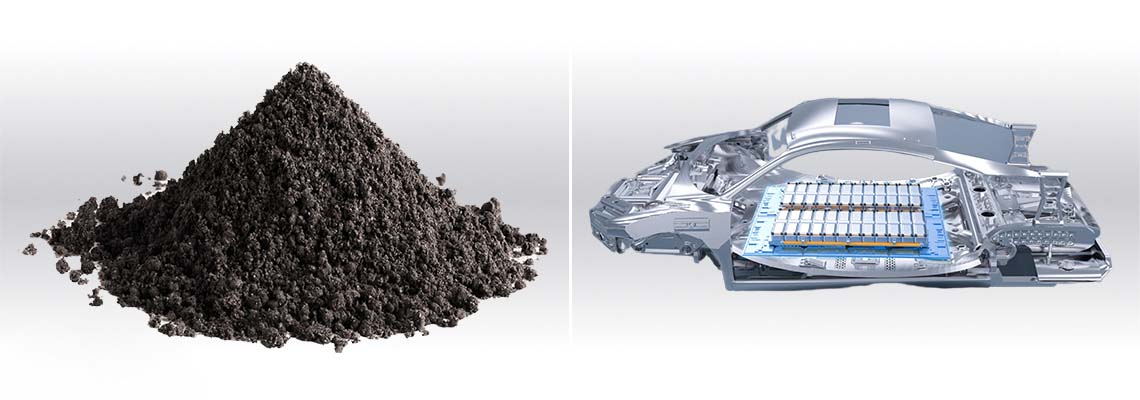
- 1. Exploración de los minerales esenciales para la fabricación de pilas.
- 2. La importancia de la trituración y la molienda en la fabricación de pilas.
- 3. Optimización de la calidad de las pilas mediante separación magnética.
- 4. Las etapas clave de la purificación de minerales: Flotación, Lixiviación, Precipitación, Filtración, Calcinación.
- 5. Reducción: Etapa decisiva para la obtención de metales puros de níquel y cobalto.
- 6. La búsqueda de la máxima pureza para unas pilas excelentes mediante el refinado electrolítico.
- 7. Palamatic Process : Pilas de alta calidad gracias a una meticulosa purificación de minerales.
La fabricación de baterías es un campo en constante evolución, y la calidad de los minerales utilizados desempeña un papel crucial en su rendimiento y durabilidad. Desde la trituración inicial hasta la separación magnética, pasando por técnicas como la flotación, la lixiviación, la precipitación, la filtración y el refinado electrolítico, descubra cómo se transforman los minerales en bruto en materiales de alta calidad.
1. Exploración de los minerales esenciales para la fabricación de pilas.
A la hora de fabricar pilas, es esencial conocer los tipos de mineral utilizados.
Los principales minerales que intervienen en este proceso son la espodumena para el litio, la pentlandita para el níquel, la cobaltita para el cobalto y la hematita para el hierro.
Cada uno de estos minerales desempeña un papel crucial en la composición de las pilas, y su purificación es un paso clave para garantizar un rendimiento óptimo y duradero.
2. La importancia de la trituración y la molienda en la fabricación de pilas.
El proceso de fabricación de pilas implica una etapa crucial: la trituración y molienda de los minerales extraídos.
El objetivo de esta etapa es reducir el tamaño de los minerales, lo que facilita la separación de los metales de los demás elementos. Gracias a una trituración y molienda eficaces, es posible obtener materiales de alta calidad para la producción de baterías de alto rendimiento y larga duración.
3. Optimiser la qualité des batteries grâce à la séparation magnétique
La separación magnética es una etapa fundamental en el proceso de fabricación de pilas. Se utiliza para separar ciertos minerales, como la hematites, mediante un separador magnético. Este dispositivo atrae las partículas magnéticas y las separa de los demás elementos presentes en el mineral. La separación magnética permite obtener materiales de alta calidad, esenciales para la fabricación de baterías de alto rendimiento y larga duración.
4. Las etapas clave de la purificación de minerales: Flotación, Lixiviación, Precipitación, Filtración, Calcinación.
En el proceso de purificación de los minerales utilizados para fabricar baterías, se llevan a cabo una serie de etapas clave para obtener metales de alta calidad.
En primer lugar, la flotación es un proceso que utiliza burbujas de aire para separar las partículas de mineral, como la espodumena, la pentlandita, la cobaltita y la hematites, de otros elementos. Las partículas de mineral se adhieren a las burbujas de aire y suben a la superficie del líquido, lo que permite recuperarlas.
A continuación, se suele recurrir a la lixiviación para los minerales de litio, níquel y cobalto. Se trata de disolver los metales en una solución ácida, separándolos de los demás elementos presentes en el mineral.
Una vez disueltos los metales en la solución, tiene lugar el proceso de precipitación mediante la adición de reactivos químicos específicos que reaccionan con los metales para formar precipitados sólidos.
A continuación, los precipitados sólidos se separan del líquido mediante filtración, donde el sólido recuperado corresponde al metal purificado, mientras que el líquido restante se denomina "lixiviación".
Por último, para ciertos metales como el litio, es necesaria una etapa de calcinación. Este proceso consiste en calentar el metal purificado a altas temperaturas para eliminar las impurezas restantes y convertirlo en una forma más estable, como el óxido de litio.
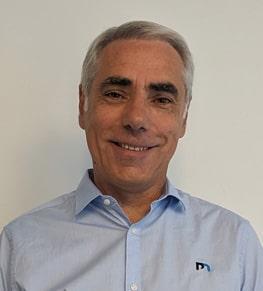
¿Tiene un proyecto de manipulación en el sector de las pilas?
Estoy a su disposición para tratar el tema con usted.
Orlando, experto en polvo
5. Reducción: Etapa decisiva para la obtención de metales puros de níquel y cobalto.
Durante esta etapa crucial de purificación, el objetivo es eliminar el oxígeno de los compuestos metálicos para obtener metales puros de calidad excepcional. La reducción se consigue exponiendo los compuestos metálicos a condiciones específicas, como altas temperaturas y la adición de sustancias reductoras. Estas últimas actúan capturando el oxígeno presente en los compuestos, favoreciendo así la formación de metales puros. La reducción da lugar a materiales altamente conductores de una pureza óptima, lo que garantiza un rendimiento superior en la fabricación de baterías modernas y energéticamente eficientes.
6. La búsqueda de la máxima pureza para unas pilas excelentes mediante el refinado electrolítico.
El refinado electrolítico es un paso clave en la purificación de metales, que permite alcanzar niveles de pureza inigualables para aplicaciones exigentes como la fabricación de baterías. Este sofisticado proceso se basa en el uso de una solución electrolítica en la que se disuelven los metales purificados. Aplicando una corriente eléctrica precisa, los iones metálicos migran al electrodo opuesto, formando depósitos de metal puro. El refinado electrolítico elimina las impurezas residuales y garantiza la calidad superior de los metales utilizados en las pilas, asegurando un rendimiento óptimo y una mayor vida útil.
El tiempo necesario para purificar los minerales varía según el tipo de mineral y el método utilizado. La maquinaria utilizada en el proceso de purificación incluye trituradoras, molinos, separadores magnéticos, celdas de flotación, filtros, hornos y celdas electrolíticas.
7. Palamatic Process : Pilas de alta calidad gracias a una meticulosa purificación de minerales.
En conclusión, la purificación de los minerales para la fabricación de baterías es una etapa esencial para garantizar un rendimiento óptimo y duradero. Las diversas técnicas utilizadas, como la separación magnética, la flotación, la lixiviación, la precipitación, la filtración, la calcinación y el refinado electrolítico, producen materiales de alta calidad y pureza excepcional.
Los expertos de Palamatic Process dominan las distintas etapas del proceso y utilizan equipos de última generación, haciendo todo lo posible por satisfacer las necesidades específicas de los clientes. Si desea obtener más información, póngase en contacto con nuestros gestores de soluciones.